GEORGIA-PACIFIC MAKES A SWITCH TO GREEN PRODUCTS
GP recently announced that all UltraStock MDF products are now manufactured using 100% No-Added-Formaldehyde (NAF) resin.
In an effort to provide more building materials for a healthy home, Georgia-Pacific has converted its UltraStock MDF (medium density fiberboard) products to be formaldehyde free.
The company announced that the company has converted all UltraStock MDF products to 100% No-Added-Formaldehyde (NAF) resin, including UltraStock Select, Premium, Lite, MR, Moulding and Embossing. Customers will no longer have to order specific “FREE-branded” products or pay extra for the benefits of an NAF board.
Physical properties, production tolerances and available board dimensions will all remain the same for UltraStock MDF with the exception that the new products’ performance in 24-hour thickness-swell testing have all improved to ≤ 5.5%, which qualifies for an MR10 designation.
Among those in the line, the company’s MDF MR products are moisture resistant, meet reduced thickness swell criteria of 5.5% or less, and meet bond integrity criteria of 50% of original MOR after accelerated aging. The Premium MDF panels are defect-free, cut and route cleanly, feature MR10 thickness-swell, moisture-resistance designation, and can be painted, printed, stained, and laminated easily. The company’s Lite MDF feature all the benefits of the Premium panels, but are also lightweight to reduce the weight of ready-to-assemble panels. The Select MDF boards are well-suited for cutting and contouring applications, such as cabinetry. The Select panels are made of highly refined fiber with a final 150 grit finish suitable for paints, stains, veneers or laminates
WEED GENERATION
Looser local laws on pot, and wider use amount to a growing challenge for construction employers who want productive, safe, and healthy jobsites.

A Gallup poll taken July 5 through 9 reaches a conclusion that one in eight American adults smokes marijuana. Among men ages 18 to 29, it’s closer to one in five.

Gallup notes:
With 29 U.S. states allowing medical marijuana use, and eight allowing recreational use, legal cannabis is taking hold in American society.
There may be obstacles to marijuana becoming fully “accepted” in the United States. Attorney General Sessions appears to be cracking down on marijuana use, and driving under the influence of pot continues to be a concern for many. Despite legal hurdles, however, a record-high percentage of Americans say they have tried marijuana.
Clearly, it didn’t take legalization, decriminalization, nor medical prescriptions to make weed a phenomenon on builders’ jobsites. It’s been a big part of the scene for years. Still, removal of laws and consequences of using makes it a cloudier dilemma for companies that employee workers who use. Three big issues converge around marijuana use and construction:
- Is it impacting skilled labor capacity?
- Does it heighten jobsite risk?
- Is today’s marijuana–with more powerful levels of psycho-active THC–a gateway to addiction to opioid based drugs?
On issue No. 1, New York Times economics correspondent Nelson D. Schwartz reports on how drug use is taking a toll on the economy by suppressing labor capacity in umpteen ways. Schwartz writes:
Even as many states decriminalize recreational marijuana use, or allow access by prescription for medical use, “relaxing drug policies isn’t an option for manufacturers in terms of insurance and liability,” said Edmond C. O’Neal of Northeast Indiana Works, a nonprofit group that provides education and skills training.
“We are talking to employers every day, and they tell us they are having more and more trouble finding people who can pass a drug test,” he said. “I’ve heard kids say pot isn’t a drug. It may not be, but pot will prevent you from getting a job.”
Many in residential construction employer positions can relate. Our own ProSales and Remodeling editor-in-chief Craig Webb researched the construction landscape, exploring how companies are addressing marijuana use in a more relaxed legal environment for a story in BUILDER’s upcoming August issue. Webb searched among large and small construction firms alike for cohesive strategies, policy, or even beliefs on marijuana use among employee associates and came up mostly empty.
Instead, company rules and policies lean toward what is expedient–being able to hire and retain workers–rather than what may be a safer, healthier course of action. Here are a select few highlights from Webb’s coming special report “Where There’s Smoke … “
- … Many empoyers continue to maintain a no-drugs policy, saying it’s the best way to ensure all remain safe. “Our policy is no illegal substances and no grace, you are fired,” declares Terry Albaugh of The Craftsmen Group, Wilmette, Ill. …
- … Tod Sakai, president of Sockeye Construction Corpo., Kent, Wash., says it’s none of his business whether his workers smoke marijuana at 7 p.m. on a work night. “But my expectation is that by 5 a.m., the next day, they need to be sober and ready to go”….
- …”Some in my peer group that do a lot of specialty work say they couldn’t hire anyone if they did drug testing,” says Gary Demos, president of Dave Fox Design-Build Remodelers, in Columbus, Ohio. “We expect a lot from our people in many ways, and it can become very difficult to add production people when we need them. So far we’re holding the line on drug testing, and I hope we won’t be forced to evaluate” ….
- …Ninety-five percent of field workers test positive every time we test,” one remodeler says. “Before we were zero tolerance, but we soon realized we wouldn’t have any workers, including some management” …
The issue of being able to hire workers–as opposed to not being able to–feels like the priority. But then what happens when someone’s safety on the site is at risk and drugs are found to be involved?
Construction, both residential and commercial, is massively decentralized and local, and that’s an impediment to traction for a clean, clear, coherent set of rules, operational mores, and workplace guidelines that protect workers’ health and safety as they earn a living.
What employers want is for associates to be “in the zone” when they’re on the job, not zoned out.
Amazon Patents the High-Rise Urban Drone-Port
Unlike warehouses on the outskirts of town, these multi-story distribution centers will be located in cities and manned by robots and drones.
BY DAVID FRANE – JUL 19
Amazon’s vision for the future includes multi-story automated distribution centers sprinkled throughout urban areas. Goods will arrive by truck and be delivered to customers by fleets of drones issuing forth from ports or doors in the building.
Few humans will work there because robots will perform much of the picking and warehousing work. At least that’s what is presented in a recently published patent application.
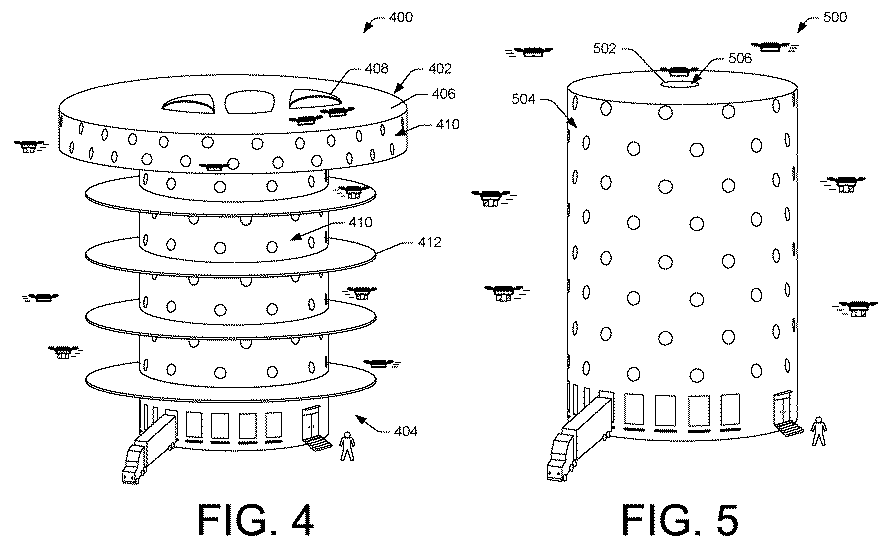
The patent documents describe these buildings as “multi-level fulfillment centers for unmanned aerial vehicles”—what we refer to as drones.
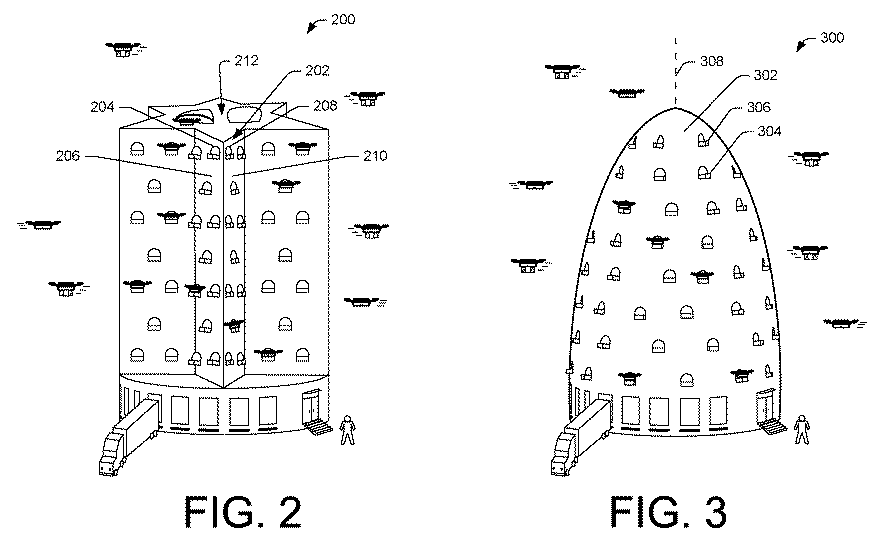
The reason for these buildings and why they need to be located in urban areas is described as follows:
Fulfillment centers are typically large-volume single-floor warehouse buildings used to temporarily store items prior to shipment to customers. Often, due to their large footprint, these buildings are located on the outskirts of cities where space is available to accommodate these large buildings. These locations are not convenient for deliveries into cities where an ever-increasing number of people live. Thus, there is a growing need and desire to locate fulfillment centers within cities, such as in downtown districts and densely populated parts of the cities.
Amazon currently uses its own vehicles to deliver some packages but most are delivered by UPS, the USPS, and others. The patent documents refer to deliveries being made with unmanned aerial vehicles (UAVs) and “short-term hired ground vehicles”. The last part probably refers to Amazon Flex, an Uber-like delivery service that is being quietly rolled out.
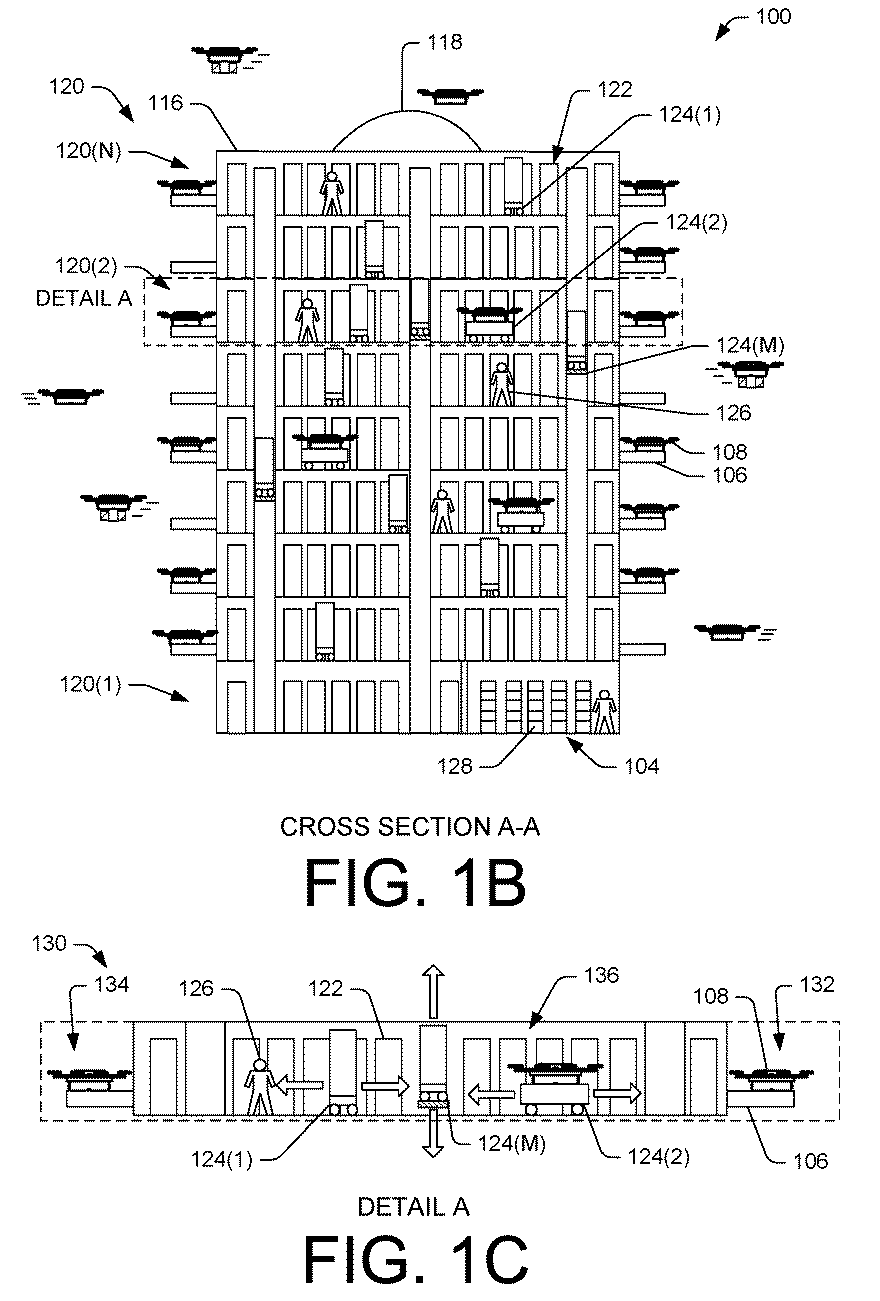
As for who or what will interact with the drone when it’s in the building the patent documents say:
…the UAV may be serviced, inspected, powered, undergo a battery replacement, be coupled to a package for deliver, and/or otherwise interacted with prior to the next flight. In some embodiments at least some of the operations may be performed by one or more robots.
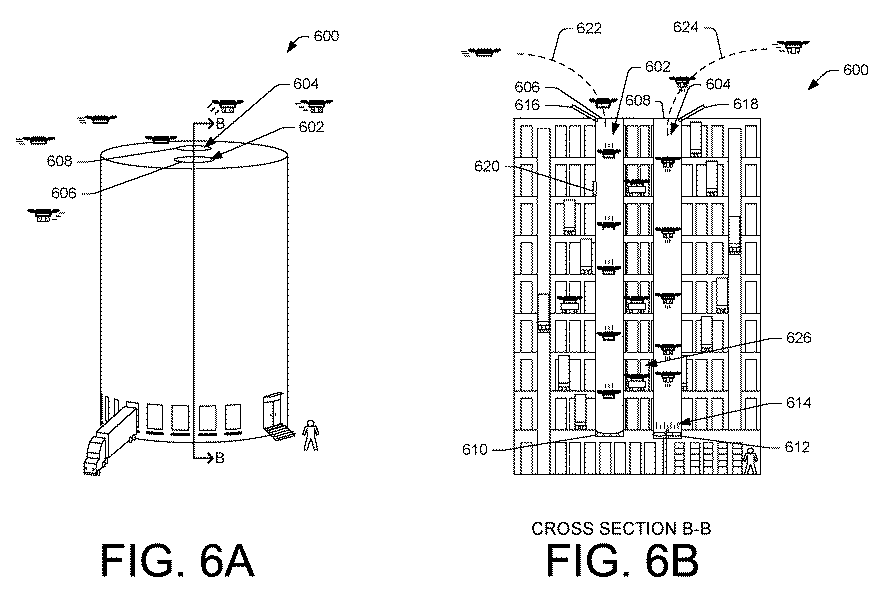
This is not the first seemingly crazy idea from Amazon. It wasn’t long ago that people thought drone delivery was nuts, and yet the U.S. Army and emergency service providers are on the verge of instituting it. One of the last big ideas from Amazon was a zeppelin-like flying distribution center from which drones could make deliveries—like the Hindenburg but hopefully without the fire.
TALL ORDER
9 best practices for large window installation.

Windows are one of the most delicate areas of the building envelope, requiring precise installation to prevent moisture intrusion, air infiltration, and energy loss. Today’s trendy, large windows and wide expanses of glass may not require many more steps than traditional units—but the larger the product, the more sensitive the installation. Mike Westfall, senior field support manager for JELD-WEN, shares nine key areas to consider when installing large windows:
- Building envelope integration. The window must be an integral part of the envelope in order to eliminate or direct air and water from the wall cavity and avoid durability issues. Westfall suggests a complete pre-installation mockup of the window and wall section with input from the full design team.
- Continuity with the weather resistive barrier. Continuity between the windows and the barrier prevents air, water, and vapor from penetrating around the window. Along with ensuring proper installation, the mockup allows the WRB representative to verify that the window installation process doesn’t void the warranty.
- Proper sealing. Not only does the sealant need to be installed thoroughly and properly, specifiers must consider the joint movement and should verify that the sealant is compatible with products it touches. Proper surface preparation is essential to ensuring the sealant works properly.
- Proper shimming. The larger the window, the more critical shimming becomes. If under-shimming occurs, it will cause sagging at the sill or head; over-shimming will lead to bowing of the jambs.
- Proper fastening. Fasteners must penetrate the structural members of the wall. Follow the schedule (spacing and number) from the manufacturer, as it is dictated by an independent third party that certified the window’s performance.
- Proper flashing. Follow all instructions and sequencing from the flashing manufacturer to ensure proper integration with the drainage plane. When installing the window, tip it in to help prevent tears.
- Proper head flashing. With large, mulled windows, drip caps are crucial to prevent water from pooling at the head and from getting behind the unit. The larger the window, the greater the potential to receive water during heavy rain loads.
- Proper pan flashing. Two of the most critical points for moisture intrusion are the two bottom corners, so follow all manufacturer instructions and sequencing. Again, tip-in installation will help ensure the integrity isn’t compromised.
- Air-tight installation. Proper air sealing provides additional redundancy to control air and water vapor, an essential step for meeting energy codes as well as the demands of homeowners.

Westfall emphasizes the importance of the pre-installation mockup, as well as the convening of the full team, including manufacturers. “There’s a lot of work behind the scenes that goes into installation of windows and doors,” he notes. “If you start out of the gate right, your potential for success is a lot better.”
WHY DESIGN AND BUILD MULTIGENERATIONAL?
As housing, medical, and education costs spiral, new single-family for-sale housing types will appeal as options.
Houses designed intentionally to be multigenerational–accommodating two adult generations of a family household living under one roof–may still be considered a fringe segment of new residential construction.
But for how long?

Pew Research tells us that one in five households in America, 60.6 million people, lived in multigenerational combinations in their homes in 2014, a number that was growing, fast, even post-Recession.
Pew analysts D’Vera Cohn and Jeffrey S. Passel further note that, while adult kids living in parents’ basements (31%) grab the sexy headlines, multigenerational living is a growing choice among aging Americans–more than a fifth live with multiple generations under one roof, including Americans ages 55 to 64 (23% in 2014) and 65 and older (21%).
Two generations ago, up through the time of the Great Depression, multigenerational living was even more common. Almost 60% of households comprised extended families. Now, many of us perceive that extended family living is a cultural choice, more prevalent in Hispanic or Asian families than white households. To some degree, population bears this out. Pew’s analysis notes:
Among U.S. Asians, 28% lived in multigenerational family households in 2014, according to census data. Among Hispanics and blacks, the share in 2014 was 25% for each group. Among U.S. whites, 15% lived with multiple generations of family members.
Think the rate of multigenerational household formation has peaked?
Think again.
Tight supply of for-sale inventory continues to put pressure on prices in more and more economically strong markets. At that same time, aging Baby Boomers are starting to enter their “grandparenting” years in droves. Boomers have tended to remap and remake markets at every turn and life stage as consumers, and among their priorities right now is real-time on-demand access to grandchildren.
It makes sense to us to believe that, for a host of reasons that are only growing more compelling and pervasive–economical, health-wise, culturally, and socially–multigenerational living will get more and more traction, especially since new construction is so hard to bring online and is therefore so expensive. Detroit-based real estate expert Mike Kalis here offers three persuasive reasons builders should put intentionally designed multigenerational living floorplans into the mix of almost every subdivision project.
Here, Trulia economics analyst Cameron Simons spotlights another whole stream of potential for multigenerational households, where two unrelated generations of adults may share a home for economic reasons. Look at today’s household balance sheets and key expenses, and you can see that economic reasons include the Big Three of consumer costs–housing, education, and healthcare.
Simons’ analysis notes big synergistic potential in the fact that many aging Baby Boom homeowners’ houses are replete with extra rooms, while many 20-somethings may be looking to get out from under mom and dad’s roof, but wouldn’t mind being under another mom and dad’s roof. Simons writes about the economic implications:

We looked at the 100 largest housing markets to find people living in homes with at least two bedrooms more than the number of occupants – to account for a guest room or office – owned by the oldest Americans. We found tens of thousands of homes have nearly 3.6 million unoccupied rooms that could be rented out.
For retired or soon-to-retire boomers, extra rooms are an opportunity to supplement income and offset cost-of-living increases – as much as an additional $14,000 a year. For many older Americans, renting a room provides an economic boost that may help them stay in a home longer.
For young adults, renting a room as opposed to a one-bedroom apartment could save them up to $24,000 annually.
And that doesn’t even count for intangible values in the arrangement, like companionship, accessibility and connectedness, etc.
Lennar’s home-within-a-home NextGen models broke new ground beyond the double-master-down floorplans that had tended to be adapted by residents into multigenerational living arrangements.
Now, Meritage Homes has partnered with BUILDER, BSB Design, and Intermark Design to push the bounds in exploring nimble, and adaptive multigenerational living arrangements, to suit primary householders with either an older or younger generation of adults living under one roof in a home.
The Meritage reNEWable Living Home aims to serve as a learning and discovery lab for engineering, design, construction workflows, on-going home system operations, and marketing and positioning, that other builders and developers can put to use in their multigenerational product development. We’ll unveil the reNEWable Living Home in January 2018 in Orlando, but you can watch the progress online and start the learning and discovery process here and now at www.builderonline.com/renewable.
PAIN KILLERS
Can and will construction come clean on the impact of substance use and abuse on its job sites, and take action to protect workers?

Like clockwork, every 10 minutes or so, 24/7, 365 days a year, an opioid or street drug overdose kills an American.
In testimony to the Senate Banking Committee about why labor participation rates among prime-age male workers is stuck in an erosive, stubborn, mystifying decline, Federal Reserve chair Janet Yellen blew her Congressional audience away recently with her conjecture.
“I don’t know if it’s causal or symptomatic of long-running economic maladies that have affected these communities and particularly affected workers who have seen their job opportunities decline,” Yellen said in response to questioning from Sen. Joe Donnelly, D-Ind., on the issue.
The United States is “the only advanced nation that I know of where in these communities we’re actually, especially among less-educated men, seeing an increase in death rates partly reflecting opioid use,” she added.
At a macro level, America’s suddenly very public health crisis around legal narcotics addiction and its tragic tie to a heroin epidemic of death and destruction have been given a key role in explaining abnormally suppressed labor participation levels across the girth of the U.S. economy. Atlanta Federal Reserve data on the 1.8 million prime-age workers currently not working for reasons due to “other” explanations shows that almost half of those individuals–881,000 people–report using an opioid the day before responding to the survey.
“The opioid epidemic is intertwined with the story of declining prime-age participation, especially for men,” says Goldman [Sachs] economist David Mericle. The crisis has created “significant costs both to employers and the public sector.”
It should come as no surprise that a scourge of such huge proportions stretches well into the economic subculture that is residential construction, both as a labor capacity issue and an outright health challenge.
“The impact of increasing number of Americans addicted to pain-killers and other drugs has resulted in lower labor force participation, particularly among Americans who have less than a four-year college degree,” says Robert Dietz, chief economist for the National Association of Home Builders. “This makes recruiting more workers into the trades that much harder.”

Digging beyond the impact of the crisis on labor participation, inquiry into the profoundly disturbing and dark world of substance use disorders–where more than 20 million Americans a year report recurrent alcohol or illicit drug use causing clinically significant impairment, including health problems, disability, and failure to meet major responsibilities at work, school, or home–the light of insight into direct connections to residential construction grows dim.
Macro data on the issue combined with a compelling correlation between occupations with high rates of physical injury, chronic pain, job security anxiety, deadline stresses, etc. and narcotic pain killer use amount to strong circumstantial evidence that home construction project job sites are not immune to the growing heart-breaking plague tearing at society’s sinews.
Ironic that in a world crushed by data, metrics on the real-world impact of America’s opioid epidemic on home building’s ecosystem of physical laborers, desk workers, Wall Street high finance players, mid-level managers and community supervisors, hard-driving sales associates, distribution and logistics specialists, well-heeled strategists and English-as-second-or-foreign-language field crews, etc. is sketchy at best.

We know that among professions and occupations, construction is one of the five top ranked fields for addictions, ranking second to mining for rates of heavy alcohol consumption, fourth in rates of illicit drug use, and second in percentage of associates who report suffering from substance use disorders.
We know too, anecdotally, that injury, pain, anxiety, and depression go hand in hand with self-medication, with the need to numb out, with a very unfair version of the game of chicken.
Put that together with the sheer difficulty of self-recognition of a problem, where the real ache or stabbing pain of an injury or chronic condition can be replaced–unbeknownst to the sufferer–by an impostor, phantom pain, that acts just like the real thing. Only it’s not the real pain at all; it’s the addiction to the pain killer at work.
Recently, we read one of the saddest, most intimate accounts of the journey into hell opioid addiction takes its victims on, and the profoundly sad toll of that pathway. It’s called “The Lawyer, The Addict.” The New York Times account’s writer, the ex-wife of a youngish high-powered attorney who died of a drug overdose, explored all the channels she could of whys and wherefores that led to this tragic end. Among the first roadblocks she encountered in her discovery process was how little real data and insight there was into the extent of substance use disorder in the legal profession. She writes:
The further I probed, the more apparent it became that drug abuse among America’s lawyers is on the rise and deeply hidden.
One of the first things I learned is that there is little research on lawyers and drug abuse. Nor is there much data on drug use among lawyers compared with the general population or white-collar workers specifically.
It’s similar in residential construction. Circumstantial evidence is strong. Hard evidence is lacking. Still, this may be one instance where waiting for the data to drive action would be a lethal, unfortunate course to take.
So we urge each and every one of you to look. To listen. To say something. To do something. Don’t wait for the data, and don’t believe for a second that the challenge only exists for the nameless, faceless, semiskilled 1099 workers on your sites. It’s up and down the socioeconomic foodchain, among many many people we care for and want to be there for.